The mixing batch size significantly affects the production capacity of a concrete factory.
In this blog, it will be explained how to choose the right mixer to both, keep the investment as low as possible and still achieve the required production capacity. The bigger the mixer, the higher the investment – this is an important fact for those who are considering investing in a concrete mixing plant, no matter which is the plant type; mobile concrete batching plant, portable concrete batching plant or central mix concrete batch plant.
Relation between mixer size and production capacity
The maximum hourly production capacity of a mixer is calculated by multiplying the maximum batch capacity of the mixer by the number of mixing cycles per hour. The duration of a mixing cycle is calculated by summing up the filling time [s], the mixing time [s] and the discharge time [s].
The batch size of a mixer does not affect the mixing time, but it affects the filling and discharge time. Filling and discharge time are becoming longer with an increasing mixer size. A bigger mixer requires more material and, as the time required for material flow does not grow linearly, it takes relatively longer to fill a bigger than a small mixer. When discharging the freshly mixed concrete from the mixer, the receiving capacity of the concrete transport equipment imposes a restriction on the discharge flow rate of the mixer and additionally, discharging a bigger mixer generally takes longer too. For these reasons, the mixer size and the maximum production capacity will not increase in direct proportion. A smaller mixer therefore allows a larger number of mixing cycles per hour than a bigger mixer.
Required amount of concrete and transport equipment available
When determining the size of the mixer, it is worth considering how much concrete is required and what kind of transport equipment is used to ship the concrete. Ready-mix concrete factories, shotcrete plants, element factories as well as block factories, they all have different demands and transport possibilities.
The required hourly amount of concrete generally determines the maximum production capacity of the mixer. However, investing in a too big mixer will not be profitable, if the mixer most the time is not producing on maximum because of only low demand for concrete.
Concrete transport equipment is also relevant when determining the mixer size. It is not worth investing in a 4 m3 mixer if only 9 m3 truck mixers are used for transport. In this case, a 3 m3 mixer would be a more cost-effective choice. It is also worth considering the number of transport equipment when determining the maximum capacity. Take into account the average driving and casting/discharging times. If there is no suitable equipment respectively no sufficient number of vehicles available, it is not worth investing in a bigger mixer.
The impact of other factors on the mixer size and production capacity
To achieve the maximum capacity of the mixer, the production has to run continuously. This means that all other equipment at the concrete mixing plant and specially the flow of raw material must be dimensioned to fit the size of the mixer. The cycle of the dosing devices must be dimensioned so, that when the previous dose is discharged from the mixer, the next dose has already been weighed on the scales. In this case, the mixer can be filled immediately after discharging without having to wait.
A concrete mixing plant also always should have a sufficient s
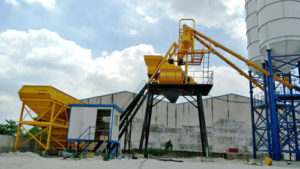
tock of raw materials for production needs. A bigger mixer is of no use if the water line does not feed water fast enough or if the production is interrupted due to the fact that one of the bins or silos is empty when the dosing takes place. When producing concrete under winter conditions, the heating system must be efficient enough in relation to the desired production capacity. All these factors must be taken into account if an investment in a new plant is planned, but especially when it comes to the renovation of a concrete mixing plant; the mixer size is only one part of the bigger picture that affects the capacity.
The mixer size and small doses
Each mixer has a minimum amount of concrete that can be guaranteed to be mixed properly. The bigger the mixer, the bigger also the minimum amount is. The deviation of the dosing devices is dimensioned according to the highest dose. The higher the deviation is, the more challenging it is to weigh small quantities with the precision required by the standards.
Summary
The size of the mixer should always be dimensioned to the needs and by looking at the whole picture. A big mixer requires also bigger plant structures and a bigger size of other equipment. The demand for the electricity, water, heating energy and the need for materials at a time will increase simultaneously. As a result of these factors, also the entire investment and maintenance costs will increase. A properly dimensioned mixer size makes it possible to keep the investment low and cost-effectively produce concrete.
Haomei machinery offers a wide range of concrete mixing plants for both, small as well as large capacity requirements. If you are considering investing in a concrete mixing plant, please contact us so we can find a suitable solution to best possibly suit your needs.
In the forthcoming blog post we’ll give you some practical tips to help you get the most out of the capacity of your actual mixer.